5 Min Read
Table of contents
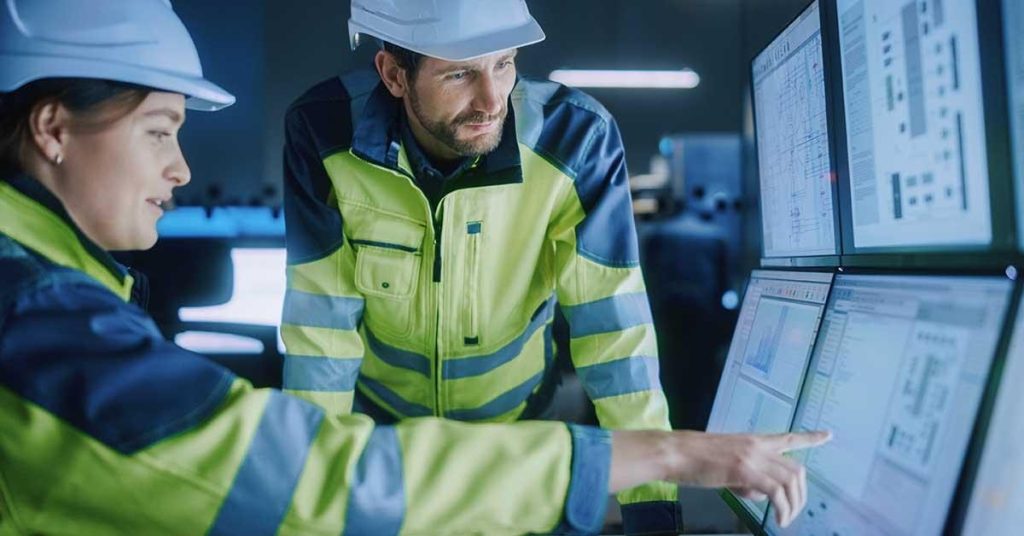
For most businesses, optimizing asset performance while minimizing maintenance costs has become more critical than ever. As equipment grows more complex and organizations aim for leaner operations, traditional maintenance strategies fall short in ensuring uptime, reliability, and compliance. Enter IBM Maximo® and its advanced Reliability-Centered Maintenance (RCM) capabilities.
IBM Maximo® RCM features, embedded within the IBM Maximo® Application Suite, enable organizations to move beyond reactive fixes and adopt predictive, data-driven, and risk-based maintenance tasks.
This article explores how IBM Maximo® RCM module empowers teams to extend asset lifespan, reduce downtime, and support operational efficiency across industries like manufacturing, utilities, and transportation.
What is Reliability-Centered Maintenance (RCM) in IBM Maximo®?
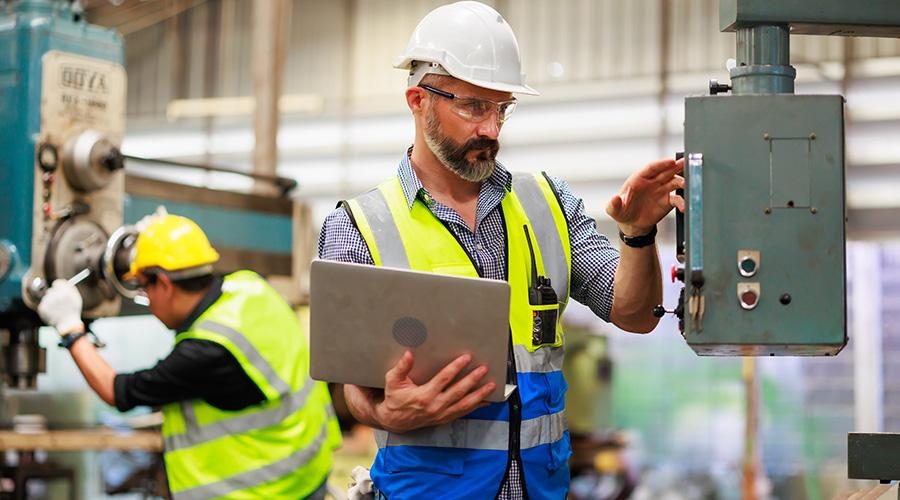
Reliability-Centered Maintenance (RCM) is a proactive maintenance strategy focused on improving asset performance by identifying potential failures, analyzing their consequences, and defining optimal maintenance tasks. Integrated into IBM Maximo® Manage, RCM enables organizations to tailor their maintenance activities based on real-time asset health, risk factors, and operating contexts.
Unlike traditional approaches that rely on routine servicing, the RCM process empowers users to develop targeted, data-driven maintenance plans that extend asset life and reduce maintenance costs.
IBM Maximo® RCM capabilities distinguish themselves through their use of features like Failure Mode and Effects Analysis (FMEA), condition-based monitoring, and risk-based planning. These tools allow maintenance teams to prioritize critical assets, automate work orders, and ensure compliance with safety and regulatory standards. Industries including manufacturing, utilities, transportation, and energy benefit from IBM Maximo® RCM by enhancing reliability, minimizing downtime, and optimizing resource allocation.
Key Features of IBM Maximo® RCM
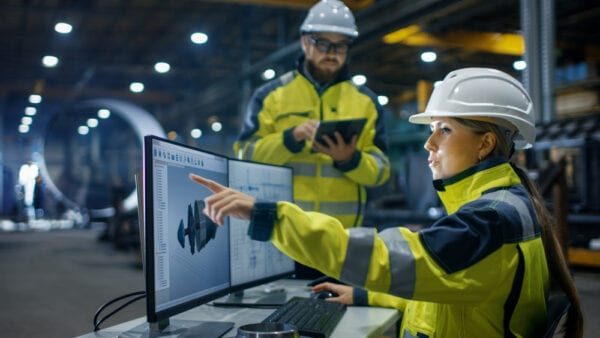
IBM Maximo® RCM is packed with intelligent features that support a proactive, data-driven approach to asset maintenance.
1. Failure Mode and Effects Analysis (FMEA)
The FMEA feature in IBM Maximo® allows organizations to perform comprehensive evaluations of assets by identifying each failure mode and its associated consequences. This structured analysis helps in understanding how assets might fail, the severity of those failures, and their potential impact on safety, operations, and maintenance costs. The integration of FMEA within the RCM module facilitates prioritization of reliability strategies and enables targeted interventions, improving overall asset reliability.
2. Risk-Based Maintenance Planning
With risk-based maintenance planning, IBM Maximo® uses asset risk profiles to determine maintenance priorities. This method balances the cost of maintenance against the operational impact and safety risks of asset failure. By assessing the probability and consequence of failure, IBM Maximo® ensures that high-risk assets receive focused attention while avoiding over-maintenance of low-risk components. This strategic planning helps reduce downtime and optimize resource allocation.
3. Condition-Based Monitoring (CBM)
CBM in IBM Maximo® Health involves monitoring real-time indicators of asset health such as vibration, temperature, and pressure. These parameters are captured using IoT devices and predictive analytics, enabling early detection of issues before they escalate into failures. This feature supports a shift from reactive to proactive maintenance, where interventions are triggered by actual asset condition rather than assumptions, significantly enhancing asset uptime and operational reliability.
4. Preventive and Predictive Maintenance Integration
IBM Maximo® seamlessly integrates preventive maintenance routines with predictive analytics to enhance maintenance precision. It automates the scheduling of inspections and servicing activities while utilizing historical and real-time data to forecast potential issues. Predictive maintenance models rely on AI and machine learning to analyze patterns and recommend optimal maintenance intervals, ensuring compliance and reducing lifecycle costs.
5. Decision Support Tools & Reporting
IBM Maximo® offers powerful dashboards and reporting capabilities through integrations like Cognos Analytics. These tools provide visibility into asset performance trends, failure frequencies, and maintenance effectiveness. Maintenance teams can prioritize tasks, allocate resources, and make informed decisions based on comprehensive reports. This feature strengthens the organization’s ability to implement continuous improvement across asset management operations.
6. Asset Criticality Ranking
Asset criticality ranking within IBM Maximo® allows organizations to classify equipment based on operational importance and failure consequences. By defining criticality levels, maintenance managers can allocate resources where they are most needed, ensuring high-impact assets receive timely attention. This prioritization helps maintain system integrity and supports strategic planning for maintenance and replacement activities.
7. Work Order Management & Integration with IBM Maximo® CMMS
IBM Maximo® RCM tightly integrates with its CMMS to automate the creation and execution of work orders. Condition triggers, risk assessments, or scheduled plans can generate work orders automatically, streamlining workflows. The system ensures that all tasks are tracked, assigned, and completed efficiently, enhancing visibility and control over maintenance processes. This integration improves task execution and helps organizations stay compliant with regulatory and performance standards.
Benefits of Using IBM Maximo® RCM
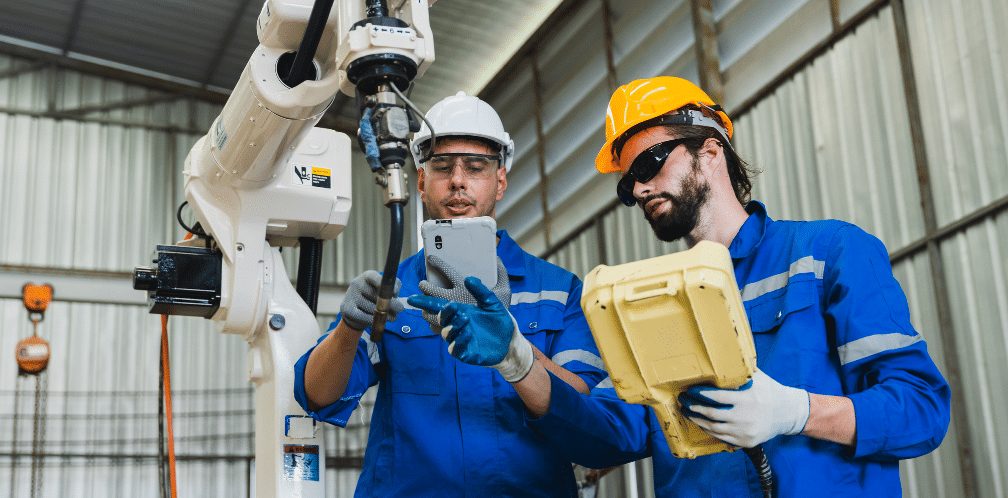
Implementing RCM in IBM Maximo® delivers tangible advantages that go beyond maintenance—driving performance, safety, and sustainability.
Reduced Asset Downtime and Unexpected Failures
By identifying and addressing potential issues before they occur, IBM Maximo® RCM significantly reduces unplanned outages. Its predictive capabilities ensure that critical maintenance is performed proactively, helping organizations maintain high levels of uptime and avoid costly disruptions.
Increased Asset Lifespan and Reduced Maintenance Costs
RCM extends asset life by applying the right maintenance at the right time. Avoiding unnecessary servicing reduces wear caused by over-maintenance, while timely interventions prevent damage that could lead to early replacements. This results in lower total cost of ownership and improved ROI.
Enhanced Workplace Safety and Regulatory Compliance
RCM emphasizes understanding the consequences of failures, particularly those that affect safety and compliance. By implementing mitigation strategies, IBM Maximo® helps ensure that assets operate safely and that organizations meet industry regulations and audit requirements.
Improved Operational Efficiency Through Data-Driven Maintenance
With features like CBM, FMEA, and decision support tools, IBM Maximo® transforms maintenance into a data-driven process. Teams can plan effectively, allocate resources smartly, and reduce unnecessary tasks, leading to more streamlined operations and higher productivity.
Support for Sustainability Goals
Optimizing asset usage reduces waste, energy consumption, and material usage. IBM Maximo® RCM aligns maintenance strategies with sustainability initiatives, supporting ESG goals and enhancing the organization’s environmental responsibility.
How to Implement RCM in IBM Maximo®
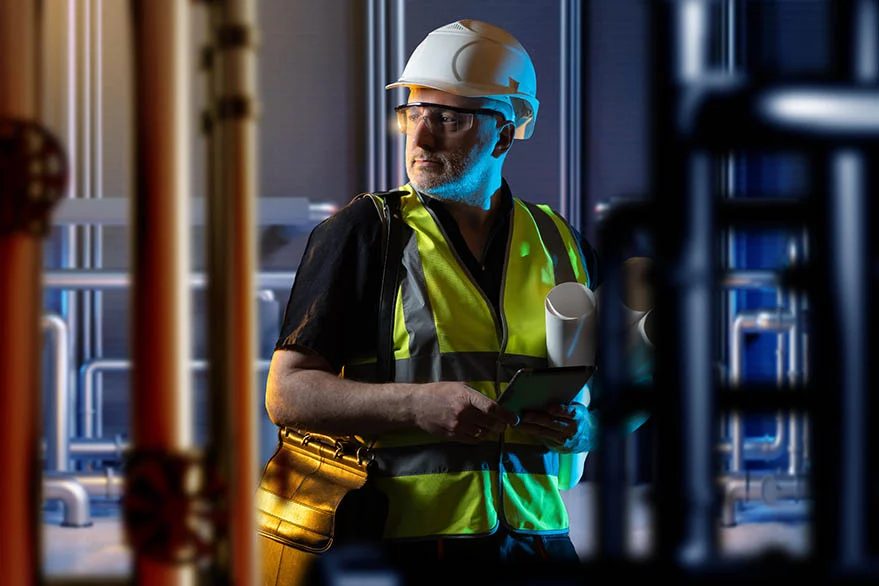
Bringing RCM to life in IBM Maximo® involves a strategic blend of planning, analysis, and technology-driven execution.
Step 1: Identify Critical Assets and Functions
- Determine which assets are vital to operations and evaluate their roles.
- Define the functions each asset performs and their contribution to business outcomes.
Step 2: Identify Failure Modes and Consequences
- Perform Failure Mode and Effects Analysis (FMEA) to determine how each asset might fail.
- Assess the consequences of failure, including safety, environmental, and operational risks.
Step 3: Develop Maintenance Strategies
- Based on FMEA, create maintenance tasks such as preventive, predictive, or corrective.
- Use RCM principles and historical data to fine-tune maintenance frequencies.
Step 4: Implement and Monitor
- Integrate RCM strategies with IBM Maximo® to manage tasks, generate work orders, and track performance.
- Leverage dashboards and analytics to evaluate ongoing asset health.
- Create a feedback loop to refine strategies based on real-world data and technician input.
Conclusion
IBM Maximo® RCM is a powerful framework that elevates maintenance from routine servicing to strategic asset management. It aligns safety, cost-efficiency, and reliability under one unified system, enabling organizations to optimize their maintenance strategies and achieve business goals.
For enterprises seeking a successful IBM Maximo® RCM implementation, Banetti is a trusted consulting partner. As a leading Enterprise Asset Management (EAM) consulting company, Banetti specializes in deploying IBM IBM Maximo® solutions tailored to your industry, assets, and goals. From configuration to training and support, Banetti ensures your RCM journey delivers measurable ROI.