5 Min Read
Table of contents
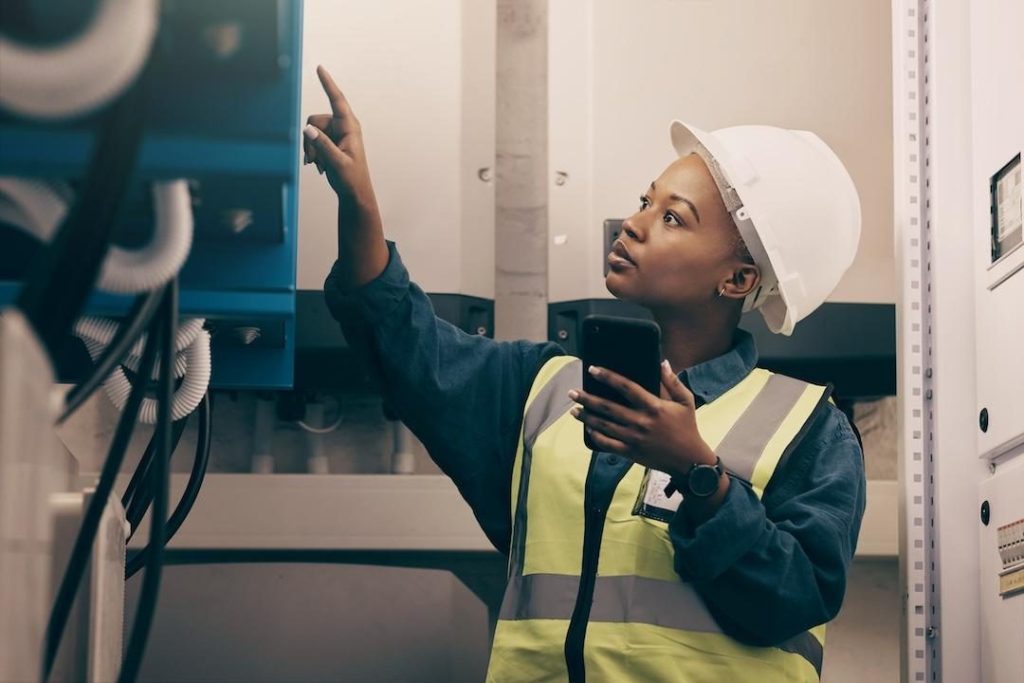
Workplace safety and regulatory compliance are critical for organizations to protect employees, maintain operational efficiency, and avoid legal penalties. Regular safety inspections help identify risks, enforce compliance, and ensure equipment reliability. However, manual inspection processes often lead to inefficiencies, data inconsistencies, and delays in corrective actions, making it challenging to maintain safety standards.
IBM Maximo® Safety Inspections streamlines the entire inspection process by automating data collection, standardizing inspection procedures, and enabling real-time tracking of compliance requirements. With digital inspection forms, AI-driven risk assessments, and seamless work order integration, organizations can conduct recurring inspections, manage multiple assets, and ensure follow-up actions are executed efficiently. The IBM Maximo® Manage Inspection forms tool enhances workplace safety, improves operational reliability, and simplifies regulatory compliance across industries.
What Are IBM Maximo® Safety Inspections?
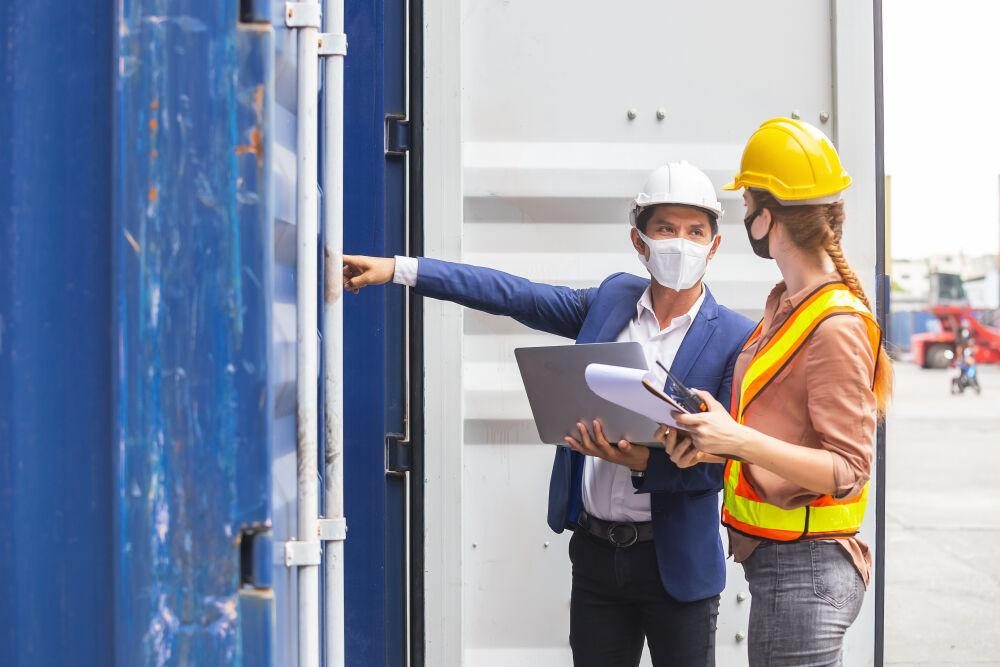
IBM Maximo® Safety Inspections is a comprehensive digital solution designed to streamline safety assessments, risk evaluations, and compliance monitoring within enterprise operations. It enables organizations to conduct, manage, and track safety inspections efficiently by digitizing inspection forms, automating workflows, and integrating real-time data collection.
These inspections cover a broad scope, including equipment safety checks, workplace hazard assessments, regulatory audits, and preventive maintenance inspections. By ensuring that all safety protocols are consistently followed, IBM Maximo® helps businesses mitigate risks, enhance workplace safety, and meet industry standards.
A key advantage of IBM Maximo® Safety Inspections is its seamless integration with asset and work management. Inspection results are directly linked to assets, work orders, and job plans, allowing organizations to take immediate corrective actions when issues arise.
Key Features of IBM Maximo® Safety Inspections
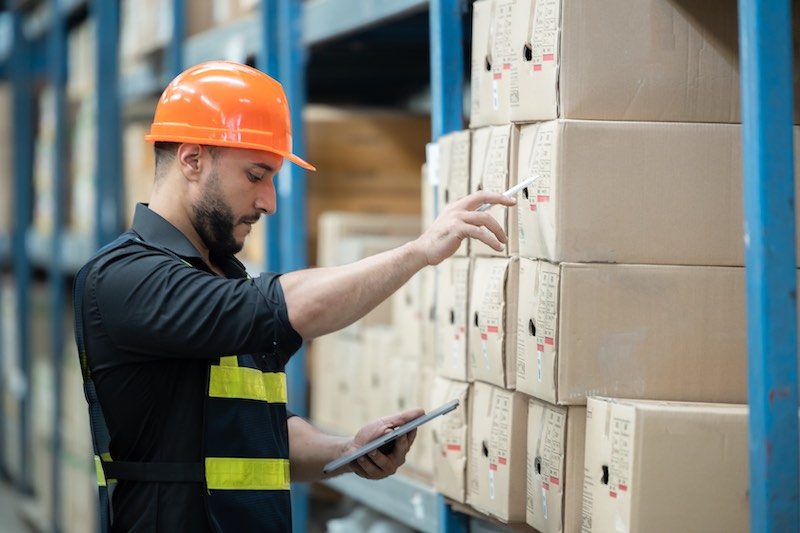
IBM Maximo® offers advanced tools like customizable forms, automated scheduling, and real-time data analysis to enhance safety inspections.
Customizable Inspection Forms
IBM Maximo® allows organizations to create tailored inspection forms that align with industry-specific safety requirements and regulatory standards. These customizable templates ensure that inspections capture all necessary data, whether for equipment checks, hazard assessments, or compliance audits. Standardized procedures enhance consistency across inspections, reducing variability and ensuring that all safety protocols are met uniformly.
Mobile Inspection Capabilities
With IBM Maximo® Mobile, inspectors can conduct on-site safety evaluations efficiently using mobile devices. The platform supports real-time data entry, photo and video capture, barcode scanning, and voice-to-text functionality, making it easier to document inspection results accurately. This mobile-first approach enhances accessibility and allows inspections to be performed in remote or hazardous locations without delays.
Automated Scheduling
IBM Maximo® streamlines inspection workflows by enabling automated scheduling of recurring safety checks. This feature ensures that mandatory evaluations are conducted on time, eliminating the risk of missed inspections due to human oversight. Automated reminders and task assignments further enhance compliance by reducing manual intervention and ensuring continuous adherence to safety standards.
Real-Time Data Collection and Analysis
IBM Maximo® provides real-time data capture and analytics, allowing organizations to assess safety risks instantly. With AI-driven insights and automated anomaly detection, inspectors can quickly identify hazards and take corrective action before they escalate. By leveraging real-time data, businesses can enhance workplace safety, improve decision-making, and maintain a proactive approach to risk management.
Integration with Work Orders
One of the most powerful features of IBM Maximo® Safety Inspections is its seamless integration with work order management. Inspection results are automatically linked to work orders, ensuring that any identified issues trigger appropriate maintenance actions. This direct connection streamlines corrective measures, reduces equipment downtime, and improves overall operational efficiency.
Regulatory Compliance Monitoring
IBM Maximo® helps organizations maintain compliance with industry safety regulations by tracking adherence to inspection requirements and generating detailed audit reports. Businesses can easily access historical inspection records, monitor regulatory performance, and ensure that all safety measures are met. This capability simplifies compliance reviews and minimizes the risk of regulatory penalties.
Benefits of IBM Maximo® Safety Inspections
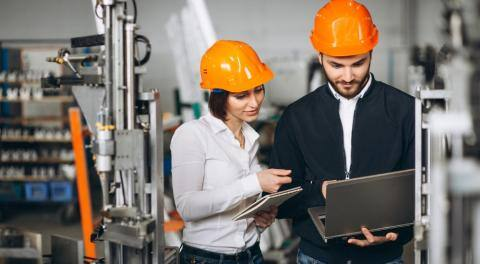
With automation, real-time insights, and seamless integration, IBM Maximo® improves workplace safety, efficiency, and compliance.
Enhanced Workplace Safety
IBM Maximo® Safety Inspections help organizations proactively identify and mitigate potential hazards, reducing workplace accidents and safety incidents. By standardizing inspection procedures and ensuring that all assets, equipment, and locations undergo recurring inspections, businesses can create a safer work environment. The ability to capture real-time safety data and implement follow-up actions ensures that risks are addressed before they escalate, enhancing overall safety and compliance.
Improved Operational Efficiency
By automating inspection forms, scheduling, and reporting, IBM Maximo® eliminates the inefficiencies of manual safety inspections. The inspection process becomes more streamlined, allowing businesses to focus on proactive risk management rather than administrative tasks. Features like mobile accessibility, real-time data entry, and integration with work records improve response times and ensure that inspections are completed efficiently. This results in cost savings and improved asset reliability, enhancing overall enterprise asset management.
Data-Driven Decision Making
IBM Maximo® enables organizations to collect, analyze, and act on safety inspection data in real time. AI-driven insights help identify trends, track inspection results, and optimize safety measures based on historical data. The ability to monitor safety performance across multiple assets, locations, and organizations ensures that leadership can make informed decisions. This data-driven approach enhances reliability and reduces maintenance issues, strengthening long-term safety strategies.
Compliance Assurance
Regulatory compliance is a critical aspect of workplace safety, and IBM Maximo® simplifies compliance tracking by maintaining accurate and accessible records. By ensuring that inspection forms, job plans, work orders, and risk assessments are properly documented, businesses can demonstrate adherence to safety regulations. Audit-ready reports, validation of inspection procedures, and revision control make it easier to meet industry standards, reducing the risk of fines or legal issues.
Industries Leveraging IBM Maximo® Safety Inspections
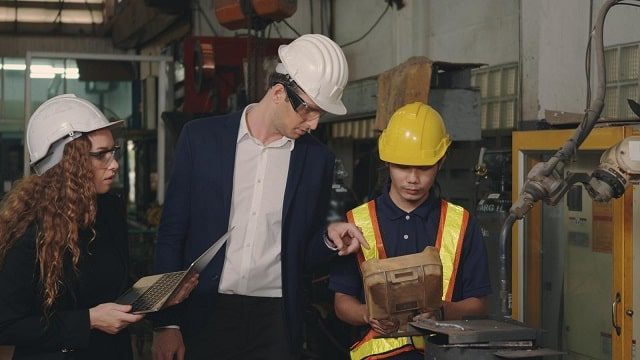
IBM Maximo® Safety Inspections is widely used across industries that require rigorous safety procedures, asset management, and regulatory compliance. Industries such as oil and gas, manufacturing, utilities, and transportation rely on IBM Maximo® to streamline their inspection processes, reduce workplace risks, and ensure real-time compliance monitoring. These industries manage complex operations involving multiple assets, recurring inspections, and regulatory mandates, making IBM Maximo® a crucial tool for maintaining safety and efficiency.
For example, Sund & Bælt Holding A/S, a leading infrastructure management company, leveraged IBM Maximo® for civil infrastructure inspections. The company automated bridge inspections using AI and real-time data collection, reducing the time and cost associated with manual inspections.
Similarly, the Advanced Manufacturing Research Centre (AMRC) adopted IBM Maximo® Visual Inspection to enhance quality control and defect detection in manufacturing, enabling AI-driven safety assessments and improving operational efficiency
Best Practices for Implementing IBM Maximo® Safety Inspections
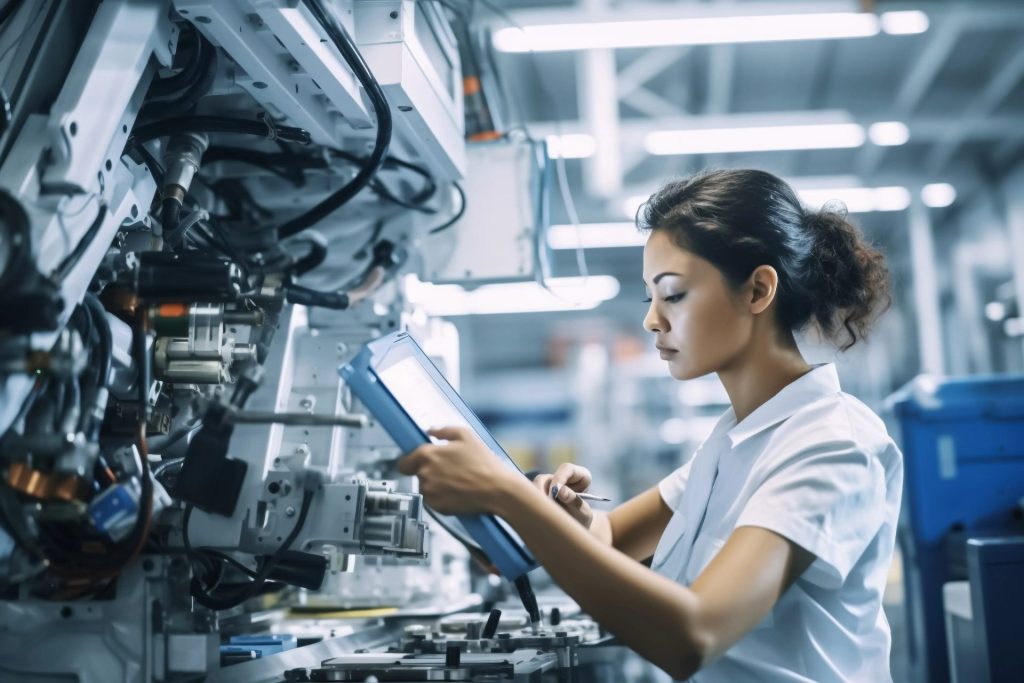
Following customized templates, training, mobile tools, and regular updates helps maximize the impact of IBM Maximo® inspections.
Customize Inspection Templates
Use the Manage Inspection Forms tool to create initial inspection forms tailored to regulatory and operational needs. Define job plan tasks, set up response types like single numeric values, and add conditions for more detailed inspections. By associating inspection forms with assets and locations, organizations can ensure consistency and compliance.
Train Personnel
Educate teams on how to complete new inspection forms, update inspections from draft status, and manage follow-up actions. Training should cover safety plan execution, using real-time data, and addressing additional questions based on inspection results to improve workplace safety.
Leverage Mobile Tools
Enable inspectors to conduct safety checks efficiently using mobile devices. Mobile tools support new inspection forms, voice-to-text inputs, and image capture, reducing errors and streamlining safety evaluations. Inspectors can also access job plans and submit findings instantly.
Regularly Review and Update Protocols
Continuously refine inspection procedures to align with evolving regulations. Update safety plans, revise job plan tasks, and use revision control to ensure compliance. By adjusting forms in draft status and modifying additional questions, businesses can keep inspections accurate and effective.
The Future of Safety Inspections with IBM Maximo®
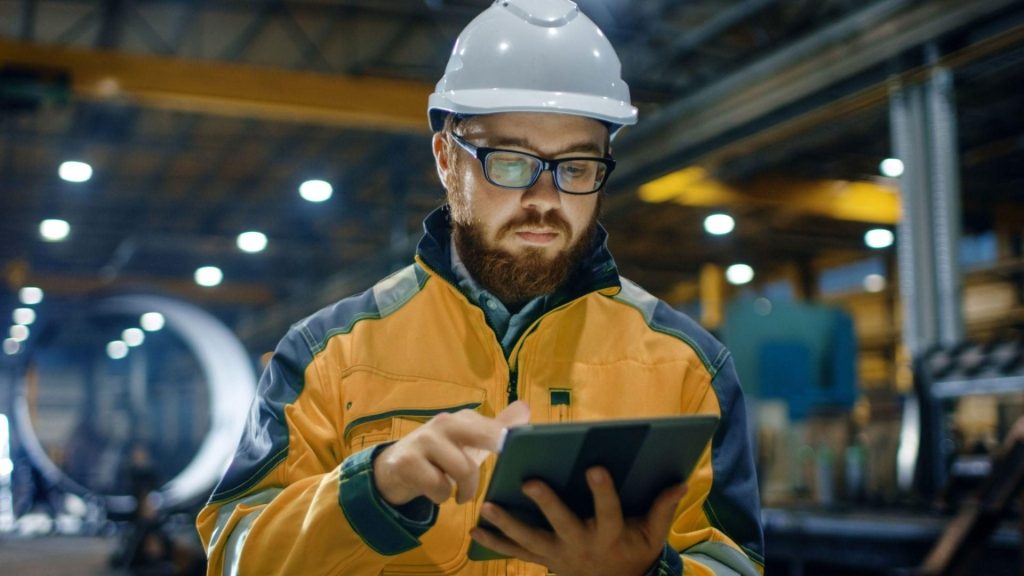
IBM Maximo® is evolving with AI and IoT integration, transforming traditional safety inspections into predictive safety management. By leveraging real-time data collection and machine learning algorithms, organizations can anticipate potential hazards before they escalate. IoT-enabled sensors continuously monitor equipment conditions, while AI analyzes patterns to detect anomalies, reducing downtime and improving workplace safety. This proactive approach enhances safety plans and minimizes risks associated with multiple assets and locations.
Advanced analytics and risk assessment tools within IBM Maximo® enable businesses to move beyond reactive maintenance. By analyzing inspection results, job plan tasks, and historical work records, the system predicts potential failures and recommends preventive measures. Organizations can automate recurring inspections, trigger follow-up work orders, and refine inspection procedures based on real-time insights. As AI and IoT continue to advance, IBM Maximo® will further streamline compliance, making safety inspections more efficient, data-driven, and reliable.
Conclusion
IBM Maximo® Safety Inspections is a powerful solution that streamlines workplace safety, regulatory compliance, and asset management. With customizable inspection forms, automated scheduling, mobile inspection capabilities, and real-time data collection, organizations can efficiently manage safety plans, job plan tasks, and recurring inspections. The seamless integration with work orders ensures that identified issues are addressed promptly, while AI and IoT-driven analytics enhance predictive safety management, reducing risks before they escalate. These features not only improve operational efficiency but also help businesses maintain a proactive, data-driven approach to safety compliance.
For organizations looking to maximize the benefits of IBM Maximo®, partnering with an expert consulting firm like Banetti can make all the difference. As a leading EAM consulting company, Banetti helps businesses implement, optimize, and fully leverage IBM Maximo® for improved safety management, regulatory adherence, and operational reliability. By adopting IBM Maximo® with the support of Banetti, organizations can ensure a safer, more efficient, and compliance-driven future.